Top Down Enterprises Inc.
HEAVY EQUIPMENT SALES AND REPAIR SERVICES IN KAMLOOPS, BC
MOBILE HEAVY DUTY EQUIPMENT MECHANIC
At Top Down Enterprises Inc., we are committed to our customers – providing quality, cost-effective service options for all makes and models of Heavy Equipment.
Serving Kamloops, Thompson-Okanagan, British Columbia, and Alberta.
For Equipment Repairs, Contact Top Down Enterprises Inc. in Kamloops, BC
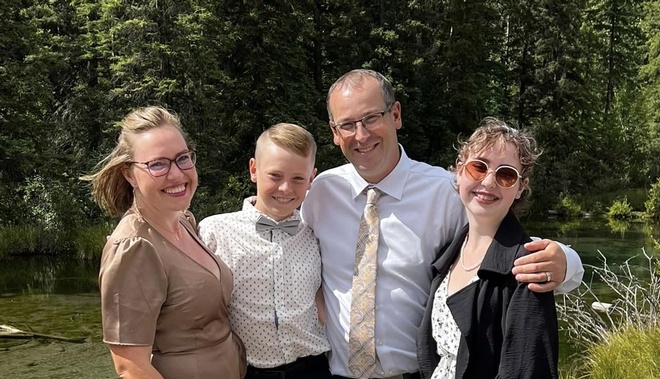
About Top Down Enterprises Inc.
Family Owned and Operated, Kamloops, BC
Top Down Enterprises Inc. is a family-owned and operated business based in Kamloops, BC. Our company was founded in 2016 with the goal of supporting HSM Forestry Machines in the establishment and implementation of safe steep slope harvesting practices. Since then, we have expanded our business to become the Western Canada Dealer for sales of the TimberMAX Traction-Winch Systems and NISULA Forest Harvesting Heads and Shears.
At Top Down Enterprises Inc., we are dedicated to providing our customers with quality, cost-effective service options for all makes and models of heavy equipment. Our team has a strong technical background and dealership training, which makes us a key contact for equipment diagnosis and repair.
We primarily provide services in BC's Interior but are open to all inquiries. Our commitment to customer satisfaction means that we go above and beyond to ensure that your equipment is running smoothly and efficiently. Whether you need repairs, maintenance, or sales support, Top Down Enterprises Inc. is here to help.